Imagine you wake up to find yourself transformed into a truck driver in the US.
You grab your cup of coffee and rush to your first appointment to load some packages from a warehouse. You’re on time, but have been asked to wait for several hours in the parking lot for your deliveries.
What’s worse is you’re made to wait frequently without any pay. If you feel frustrated, that’s the grave reality that drivers face everyday.
Every minute under the roof waiting to hit the road is bad for end customers, bad for drivers who don’t get paid, and bad for business if customers start to lose their trust en masse.
But there’s a fix. Let’s drive in!
What is time under the roof?
The total time that drivers have to wait at warehouses while loading or unloading packages is called time under the roof. All Third Party Logistics (3PL) and Courier, Express and Parcel (CEP) businesses express time under the roof in terms of metrics like dwell time and detention time.
Dwell time is the minimum amount of time that drivers have to spend to drop-off or pick up loads from warehouses or fulfillment centers. But detention time is the time spent beyond dwell time at warehouses to load/unload packages.
If dwell time is within the set threshold limit of a company, then:
Time under the roof = Dwell time
But when dwell time increases beyond a threshold limit, then it is counted as detention time.
Time under the roof = Dwell time + detention time
CEP businesses should make sure that dwell time stays within their set threshold limits for drivers to be more productive. If dwell time breaches that limit, then any extra time becomes detention time, which kills productivity of fleet drivers.
If time under the roof should be low, dwell time should stay within the threshold and this threshold varies between businesses.
Time under the roof:
The biggest threat to driver satisfaction
The CEP industry is currently undergoing a transformative phase, and its growth prospects appear promising. According to a survey, the global package shipping volume reached 159 billion packages in 2021, and this number is projected to soar to 256 billion packages by 2027.
While this is positive news for the industry's overall expansion, experts and industry stakeholders express concerns about a driver shortage that could result in a capacity crunch for fulfilling these orders. However, Dr. David Correll from MIT FreightLab offers a different perspective.
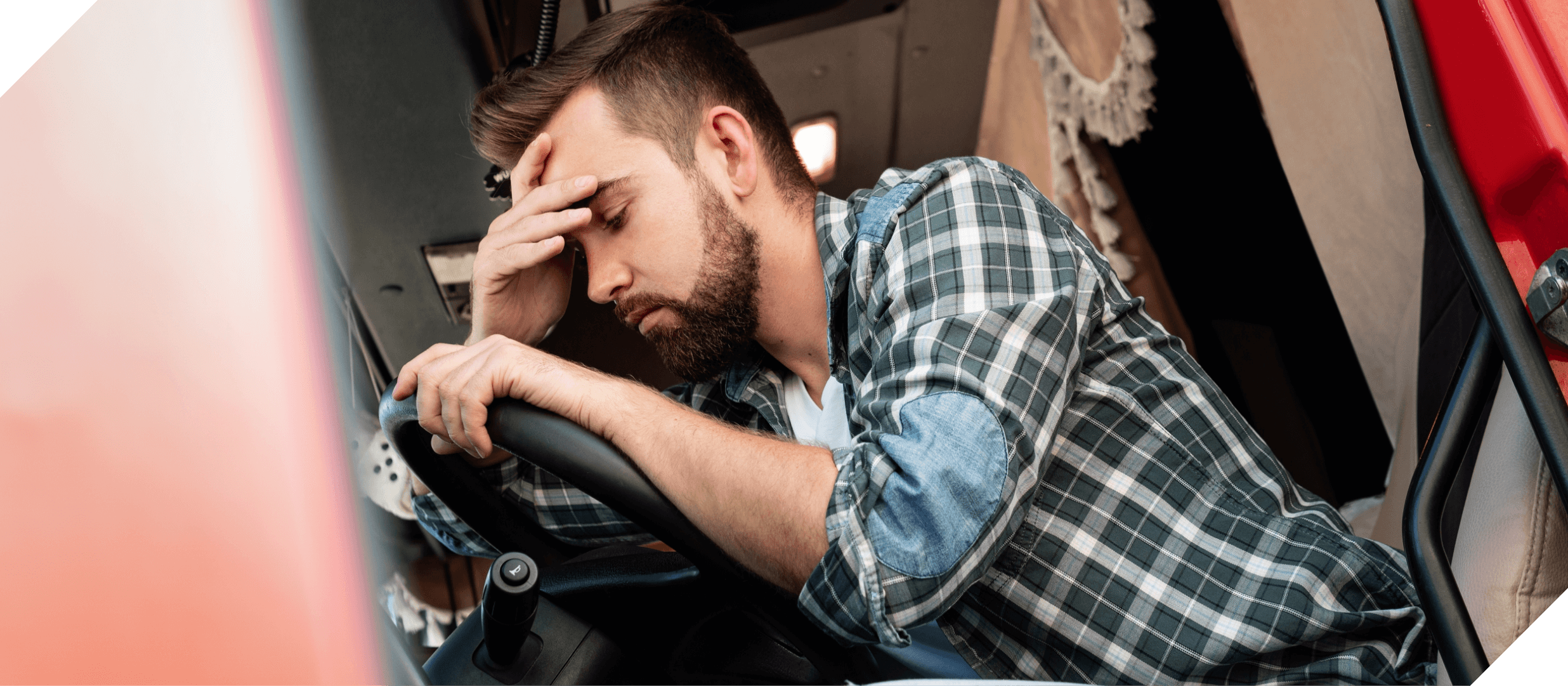
Dr. David points out that longer wait times for drivers at warehouses lead to the underutilization of their time. He emphasizes that, out of the legally allowed 11 hours of daily driving for commercial truck drivers in the United States, they spend a maximum of six and a half hours on the road. These statistics indicate that drivers are compelled to allocate 41% of their total driving hours to idle time or time spent under the roof, waiting at warehouses for loading and unloading packages.
Furthermore, when time under the roof consumes drivers' time, it intensifies the pressure to make on-time deliveries, which, in turn, increases the risk of accidents. A survey conducted by the United States Department of Transportation (DOT) reveals that a 15-minute increase in the time spent by trucks waiting at a facility results in a 6.2% rise in the expected average crash rate.
Another critical issue is that drivers do not receive compensation for the time they spend waiting at receivers. Even if some carriers charge for time spent under the roof, the amount paid is often insufficient to cover the cost of the driver's lost time.
In summary, an increase in time spent under the roof has a detrimental impact on drivers' productivity and morale, leading to a decline in driver retention. If you are a CEP business seeking to enhance driver retention, it is imperative to prioritize the reduction of driver detention.
What can CEP businesses do to reduce the time under the roof?
With increased order volumes and rising logistical complexities, managing driver productivity has become a grueling task. Today, every second a driver spends on the road counts as it makes a big difference in the business growth.
A burning question for all CEP businesses is what to do to minimize the time under the roof. Read on to find out what steps a business should take to cut the rising time under the roof.
Looking to bring down the time under the roof?
Schedule a demo now!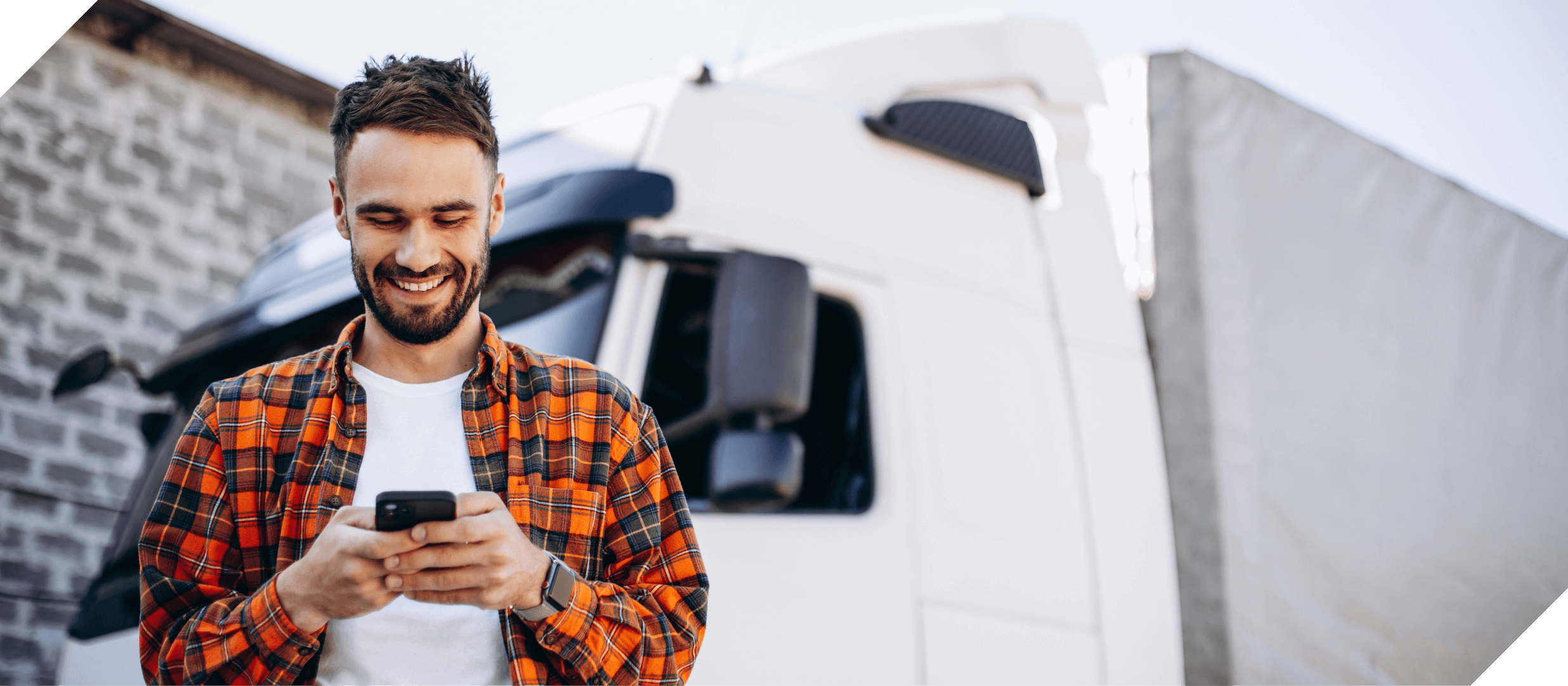
Make Use of Analytical Insights
A pre-pandemic study highlighted that detention time reduces drivers’ annual earnings to $1.1 or $1.3 billion. This results in a reduction of drivers’ average annual income between 3 and 3.6%.
How do we bridge this gap of drivers' incomes caused by time under the roof? The answer lies in data.
It becomes difficult to track and measure time under the roof without the help of data. Let’s say that delayed arrivals for a couple of trucks are increasing time under the roof for other vehicles. If a business wants to know why delayed arrivals are increasing and solve for it, they need strong analytics capabilities to bring out the hidden inefficiencies.
Using technologies like dispatch management software, businesses can identify analytical insights on driver arrival time, wait times, and time the truck leaves the warehouse. This data helps them plan vehicle and driver shifts, and prevent delays in advance. It even helps them account for probable rainy days, holidays, and sick days, and secure delivery capacity when it’s most needed.
With its comprehensive insights on driver/vehicle level, dispatch management software helps delivery businesses find if drivers are on time to the warehouse after completing their trips. This helps them rework the driver schedules efficiently and reduce the time under the roof.
Want to leverage analytics to minimize time under the roof?
Schedule a demo now!Elevate Efficiency at Hubs
In the ever-evolving landscape of modern logistics, the efficient handling and sorting of packages have emerged as a fundamental challenge for businesses. Beyond the initial scanning of packages, the subsequent sorting, load formation, and picklisting process stands as a pivotal step in the supply chain. However, this crucial phase involves a multitude of complex factors, including delivery speed, order nature, service zones, time windows, and order preferences, all of which must be meticulously considered. Even the slightest inefficiency at this stage can have far-reaching consequences, leading to confusion in orders allocated to different vehicles and drivers.
Therefore, in this context, investing in advanced package-sorting solutions has become imperative. These innovative systems are designed to automate scanning, sorting, load formation, and picklisting. By embracing such solutions, businesses can achieve a profound impact, including:
- Time Efficiency: Automated sorting drastically reduces the time required for this critical operation, ensuring that packages move swiftly through the distribution center.
- On-road Productivity: By minimizing the time packages spend under the roof, businesses can enhance the productivity of their drivers, meeting tight delivery schedules and ensuring prompt order fulfillment.
- Precision: Automation eliminates the potential for human errors in the sorting process, significantly reducing the occurrence of incorrect deliveries and related customer complaints.
- Cost Savings: While the initial investment in parcel sorting solutions may seem significant, the long-term benefits, including reduced labor costs and enhanced operational efficiency, make it a financially prudent choice.
Optimize Routes and Schedules
Earlier, many CEP businesses tried to provide appointments to truck drivers to minimize inefficiencies in delivery management, which did little good.
Every vehicle might deal with hundreds of deliveries and loading them definitely takes time. If the sorting process is inefficient, it will increase the number of vehicles lined up outside the warehouse.
It is critical to reduce the sorting time and make it more efficient to minimize the time under the roof. But how’s it possible? By optimizing the routes and driver schedules, businesses can maximize sorting efficiency.
What happens when businesses optimize driver schedules and routes?
- Driver check-in time gets aligned with customer-preferred time windows
- Assign loads to drivers in certain delivery zones that needs first-preference
- Plan return check-in times of drivers and prepare loads for it
- Minimizes the chances of missed deliveries for subsequent trips
If all this has to happen, then businesses should ensure that the route planning is efficient and accurate.
When route planning is inefficient or manual, drivers find it exhausting to complete their delivery targets over time.
By using route optimization software, businesses can plan routes so that drivers have plenty of time to complete their deliveries. As drivers deliver parcels on time, they can get back to the warehouse at the expected queue time. Beyond increasing the on-time delivery rates, route optimization software improves the predictability of drivers’ arrival times to warehouses.
Do you want to know how to improve your on-time delivery performance?
Read it hereImprove Visibility and Communication
Let's consider a scenario where a business regularly receives complaints from customers about delayed deliveries. Upon investigation, they discover that the primary reason for these delays is the busiest time at the warehouse.
To gain a better understanding of these frequent delivery delays caused by increased time under the roof, they pose some critical questions:
- Which delivery zone has the highest number of customer complaints?
- Which vehicles are responsible for these delays?
- Which loading/unloading time slot in the warehouse contributes significantly to delivery delays?
- How often do drivers request schedule changes due to unforeseen circumstances such as severe weather, accidents, traffic congestion, vehicle issues, or roadblocks?
The answers to all of these questions revolve around visibility and communication!
Through enhanced visibility and communication, businesses can easily monitor the current status of loads and their wait times. This improvement facilitates collaboration among dispatchers, warehouse executives, and fleet drivers. Even in cases where there are changes in driver check-in times due to unforeseen events, businesses can incorporate them into load assignments. This enables them to plan and reschedule loading/unloading times in advance, ultimately minimizing the time spent under the roof.
Optimizing Volume Utilization
Volume utilization is a critical element in warehouse operations, crucial for reducing time spent in the warehouse. It extends beyond merely maximizing vehicle space efficiency.
Imagine an instance in a warehouse where a package is mistakenly placed deep within a delivery vehicle intended for the first customer. Correcting this error results in extended warehouse time as orders must be rearranged within the vehicle.
To enhance volume utilization, efficient load formation and load balancing are essential. Load formation assigns orders to suitable vehicles or pallets, while load balancing organizes orders within vehicles, following the Last-in First-out and First-in Last-out principle. This ensures the package for immediate delivery is accessible and the last to be delivered is placed deep inside the vehicle.
By adhering to these practices, warehouse businesses can improve volume utilization, reduce delivery vehicles, and minimize time spent under the warehouse roof, enhancing overall efficiency and cost-effectiveness in logistics operations.
Want to know how Locus can boost your profits?
Less time under roof means optimal deliveries on the ground
It may sound like an overstatement, but it is true: drivers are the on-ground logistics warriors for delivery businesses. When they don’t plan, track, and optimize the time under the roof, drivers become dissatisfied. Increasing dissatisfaction among drivers results in higher driver attrition. Consequently, it makes driver retention more challenging.
The best way to counter issues with time under the roof for drivers is by investing in technology like a dispatch management platform.
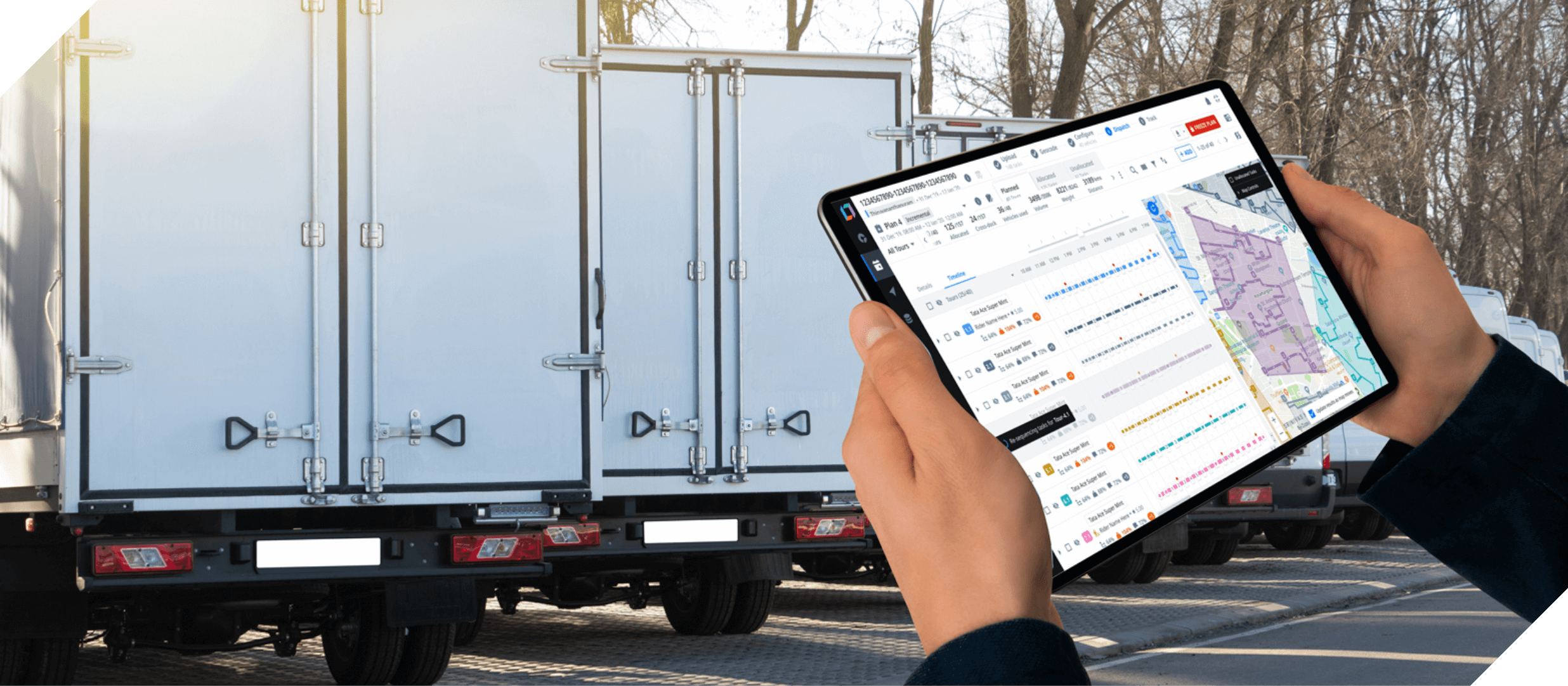
Locus is an integrated dispatch management platform specializing in solving the issues that arise in all-mile logistics. Its dynamic algorithms and insights help businesses effectively plan, track, and schedule wait times for trucks in warehouses. Its route optimization feature generates routes that maximize deliveries and enables drivers to spend fewer hours on the road, minimizing time under the roof.
Locus' offerings enable CEP businesses to optimize their hub operations. These hub operations involve scanning, sorting, load formation, picking, and trip completion. With its automated load balancing and sorting capabilities, Locus’ platform enables first-in-last-out and last-in-first-out loading operations. Its intelligent algorithms help sort orders strategically to ensure a faster dispatch process, reducing wait times and improving the delivery performance of the fleet.
A critical functionality of Locus’ dispatch management platform is its advanced load formation capabilities. Using its integrated load formation capabilities, it efficiently assigns orders to the most suitable pallet or truck, maximizing volume and cost efficiency while reducing the number of vehicles used. This cuts down on the fuel costs involved and makes delivery operations more sustainable.
With its centralized hub-level control, Locus’ end-to-end dispatching platform simplifies end-of-day settlement for each trip. It enables businesses to reconcile payments, track orders, recover assets at hubs, and manage undelivered SKUs. This eliminates unauthorized movements and reduces delays caused by missing items and misrouted orders.
Most importantly, Locus’ dispatch management platform uses an intelligent sorting engine. It automatically sorts orders based on time windows, service zones, delivery speed, order priority, vehicle capacity, and driver skill sets. This improves dispatch planning, speeds up order fulfillment, and minimizes the time that delivery vehicles spend at the hub.
With a parcel sorting module integrated with geocoding, Locus’ dispatch management platform helps businesses predict loading/unloading times based on which zone orders need to be delivered first. This allows them to effectively plan and prioritize drivers' return check-in times at warehouses, thereby minimizing time under the roof.
Is time under the roof making your logistics operations costly and complex?
Resources
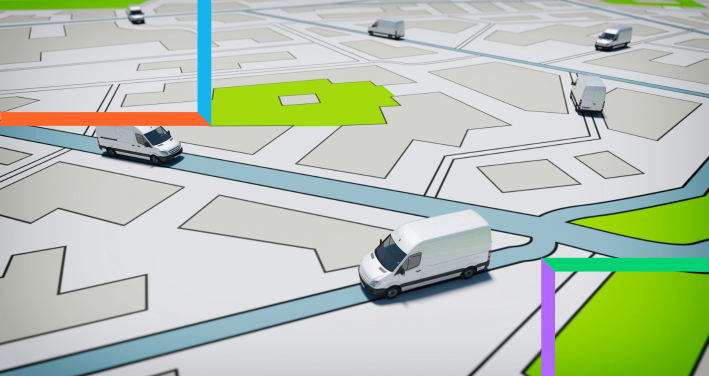
Blog
Multi-stop route planning and why is it important?
Planning multiple routes manually is a burdensome and time-consuming affair. Fleet managers should factor in various route constraints while planning routes such as traffic congestion, roadblocks, and so on. There are likely chances of making mistakes, which can ultimately result in disappointed customers.
Read more